目次
製造業AI導入の現状と課題
日本の製造業では AI 活用が徐々に広がりつつあるものの、本格導入は依然として限定的です。
2025 年3月に公表された MMD 研究所の大型アンケートでは、製造業で「AI を実運用している」と回答した企業は 21.4 % にとどまりました 。さらに企業規模を絞ると、楽天×エデルマンが 2024 年末に行った調査では 中小企業の導入率が 16 % 前後 に過ぎず 、帝国データバンクの生成 AI 動向調査でも 17.3 % という類似の水準が報告されています。
導入が進まない背景には、初期投資コストの高さ、運用習熟に要する時間、そして AI 人材・データリテラシーの不足が依然として大きな壁となっていることが、これらの最新調査でも繰り返し指摘されています。
製造業におけるAI活用の主な障壁は、以下の通りです。
- 導入コストの高さ:産業用ロボットやAIシステムの初期費用は数百万円から数千万円と高額であり、中小企業にとっては大きな負担。
- メンテナンス・運用負担:システム導入後も、定期的なメンテナンスやアップデートに継続的なコストが発生。
- オペレーション習熟の難しさ:AIやロボットの操作には一定のスキルが必要で、教育や訓練に時間がかかる。
- デジタルリテラシー不足:製造現場の多くで、AIやITツールに対する抵抗感や知識不足が依然として強い。
こうした要素が重なり、日本の製造業では「人間の方が安上がり」と判断される場面が多いのが実情です。特に中小企業では、限られたリソースの中で短期的なコスト削減を重視する傾向があり、AI導入は慎重にならざるを得ません。
一方で、製造業DX(デジタルトランスフォーメーション)の推進は政府レベルでも強く後押しされており、企業変革力を高めるためにもデジタル技術の活用が不可欠だと認識されています。
今後、少子高齢化による労働力不足や、国際競争力維持の必要性から、AI導入は避けられない選択肢となっていくでしょう。しかし、現時点では多くの企業にとって「まだ人間の方が安い」というコスト構造が続いていることを理解しておく必要があります。
製造業自動化のコスト動向と将来予測
製造業における自動化のコストは、ここ十数年で着実に低下傾向を示しています。特に、産業用ロボットや協働ロボットの普及によって、初期導入コストが下がり、より多くの企業にとって選択肢となりつつあります。
協働ロボット(コボット)の本体価格はメーカーや可搬質量によって幅がありますが、2024~25年現在の国内実勢では 100 万~500 万円がボリュームゾーンです。さらに、中国 FAIRINO など新興メーカーの小型機では 最小構成で50 万円前後、教育・実験用途に機能を絞ったモデルでは 30 万円台といった超廉価製品も登場し、100 万円を切る選択肢が現実的になっています。
産業用ロボットの平均価格も急速に低下しています。IFR統計をもとにした最新分析によると、世界平均価格は2010年の約 46,000 USD から 2017年には 27,000 USD に約41 %下落しました。部品共通化と市場参入の増加によりこのトレンドは加速しており、2025年には 1 万ドル台へとの予測もあります。足下の北米調査でも、標準的な新規システムの価格帯は 20,000~100,000 USD 程度が中心で、依然として下落傾向が続いています。
自動化コストの内訳は主に以下のようになります。
- ハードウェア購入費用:ロボット本体、周辺装置
- 設置・インテグレーション費用:既存ラインとの接続、カスタマイズ
- メンテナンス・サポート費用:保守契約や修理、ソフトウェアアップデート
- 教育・トレーニングコスト:オペレーターの操作習熟支援
近年では、これらすべてをパッケージ化し、サブスクリプション形式(RaaS:Robotics as a Service)で提供するモデルも登場しています。月額利用料にメンテナンスやアップデートを含むため、初期投資を大幅に抑えられる点が特徴です。
また、ロボット自体の進化もコスト構造に影響を与えています。たとえば、自己診断機能や予知保全技術を搭載したロボットでは、突発的なダウンタイムが減り、運用コスト全体を引き下げる効果が期待できます。
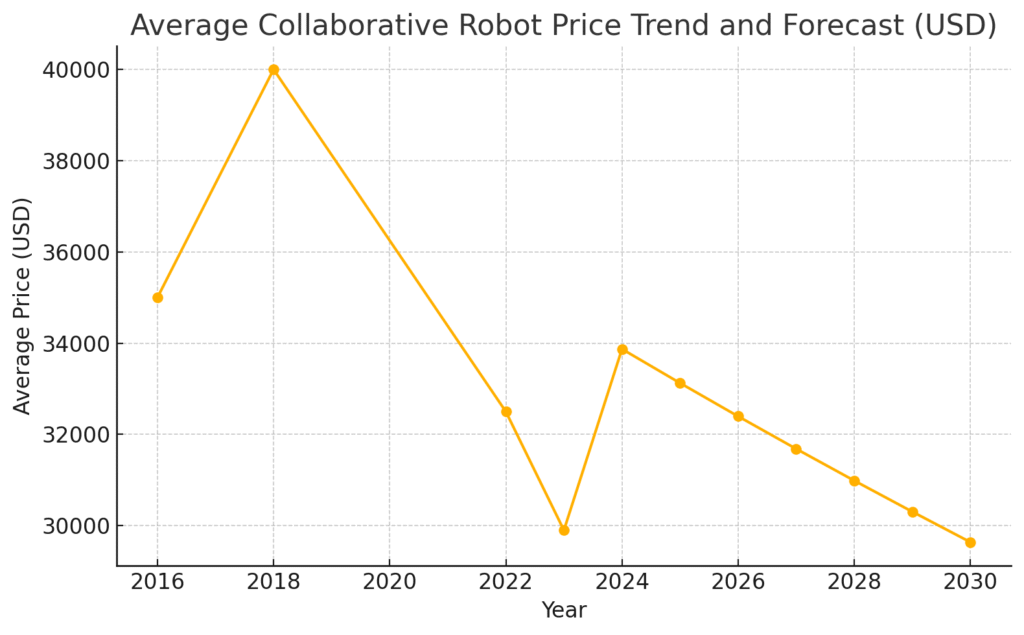
さらに、AIアルゴリズムの性能向上により、ティーチング(動作教示)作業の自動化が進み、専門知識なしでも短期間でロボットを稼働させることが可能になりつつあります。この進化により、教育コストも相対的に低下していくでしょう。
将来の予測としては、複数のレポートが「2030年前後には人件費と自動化コストが拮抗する」と指摘しています。つまり、人件費と同額か、それ以下でロボットを稼働させられる時代が到来すると見込まれています。
人手不足対策としてのAI活用とリテラシー問題
日本の製造業では、人手不足が深刻化しています。生産年齢人口(15~64 歳)はすでに減少局面に入り、IPSS「日本の将来推計人口(令和5〈2023〉年推計)・出生中位/死亡中位シナリオ」によれば、2030 年には約 6,725 万人、2040 年には約 5,735 万人まで縮小する見込みです。
こうした急速な母集団の縮小を受け、製造業各社は単なる賃上げや採用強化だけでは解決できない構造的な人材不足に直面しつつあります。
この危機に対応する策として、AI導入や自動化推進が強く求められています。実際、政府や経済団体も、製造業におけるデジタル技術活用を産業競争力強化の柱に位置づけています。
しかし、ここで大きな課題となるのが、現場のリテラシー不足です。
製造業の現場では、以下のようなリテラシーギャップが存在しています。
- ITツールやデータ活用への抵抗感
- AI・ロボティクスの基礎知識不足
- 従来型業務フローとのミスマッチ
- デジタル教育・研修体制の遅れ
総務省の調査によれば、日本企業におけるAI導入失敗の要因の一つに「運用人材の不足」が挙げられています。せっかく高額なAIシステムを導入しても、使いこなせず宝の持ち腐れになるリスクが常に伴うのです。
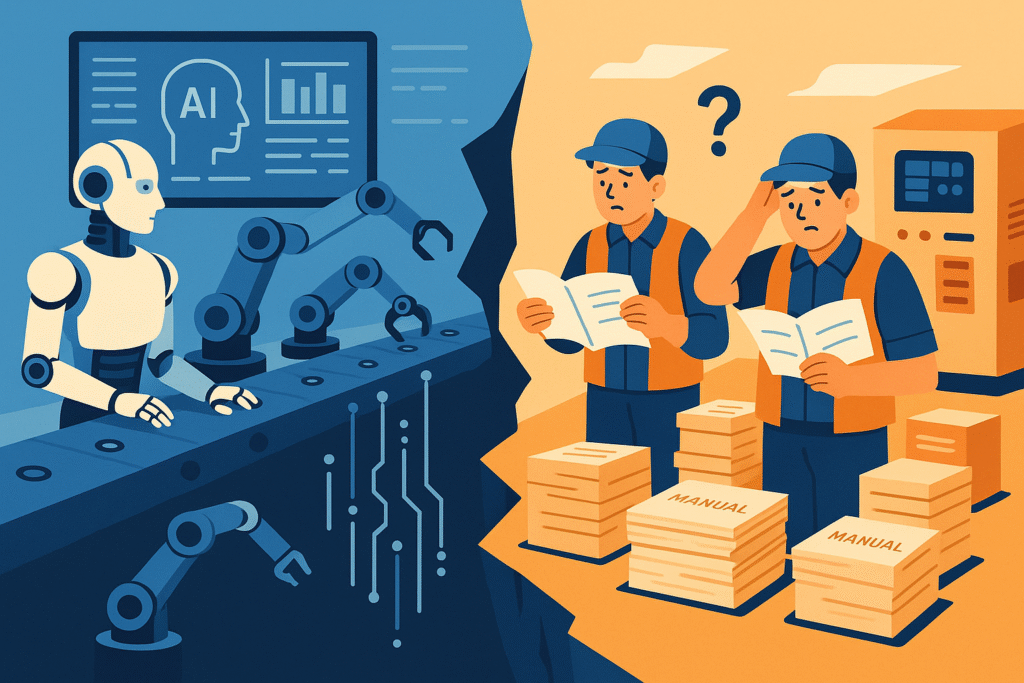
ただし、最近ではリテラシー向上に向けた取り組みも進み始めています。
具体的には、
- 製造業向けDX人材育成プログラムの整備
- 現場オペレーター向けに直感的な操作インターフェースを持つロボットの開発
- リスキリング(学び直し)支援制度の導入
などが広がりつつあります。
さらに、デジタルネイティブ世代が労働市場に参入してくることにより、現場のITリテラシー底上げも期待されています。若い世代の感覚を活かしながら、経験豊富なベテランとデジタル技術を橋渡しする新しい現場づくりが重要になるでしょう。
今後、単にAIを導入するだけでなく、「いかに現場で活用できる状態にするか」という視点が不可欠です。リテラシー向上は、人手不足対策における最重要テーマの一つとなっています。
2030年問題とAIコスト逆転のタイミング
2030年問題とは、生産年齢人口の大幅な減少により、各産業で労働力不足が深刻化することを指します。製造業においても例外ではなく、現場の担い手が減少することで、生産維持そのものが難しくなる懸念が高まっています。
これに伴い、人件費の上昇圧力も年々強まる見込みです。
経済産業省や民間調査機関のレポートによれば、2030年時点で日本全体の労働力不足は最大644万人規模に達する可能性があるとされています。製造業においても、単純作業や3K職場(きつい・汚い・危険)を中心に、人手確保が困難になることが予測されています。
一方で、前章までに述べた通り、ロボットやAIの導入コストは着実に低下しています。
厚生労働省の賃金統計と Persol×中央大学の 2030 年賃金上昇シナリオを掛け合わせると
- 製造業フルタイム労働者の総コスト(給与+企業負担社会保険料)は 630〜700 万円/年程度に達すると見込まれます。
- 一方、産業用ロボットは本体+統合費 1,000〜2,000 万円クラスが主流です。
- 8〜10 年の償却・保守・電力を含めた TCO は 200〜400 万円/年が一般的です。
- したがって早ければ 2028 年前後、遅くとも 2030 年代前半には多くの工程で人件費とロボット費が逆転する可能性が高いです。
このため、2030年を境に、
「人間を雇うよりも機械を導入した方が安い」
という判断が、多くの企業で現実味を帯びてくるでしょう。
特に、以下の分野ではコスト逆転が早く進むと考えられます。
- 単純反復作業(例:組立、検査、搬送)
- 危険作業(例:高温、高所作業)
- 夜間・休日シフト業務
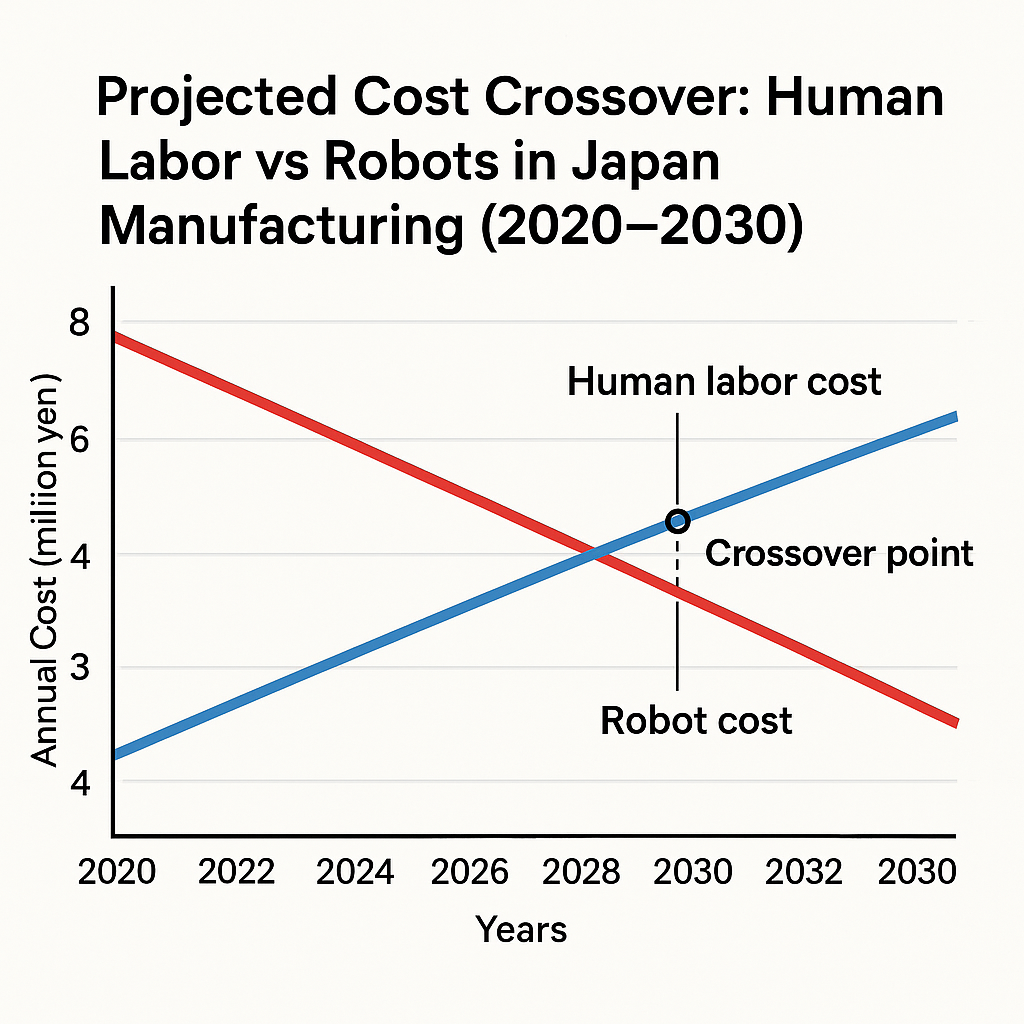
また、政府もこうした変化を見越し、
省人化投資促進税制やAI導入補助金といった政策支援を積極的に展開しています。
【2030年問題に向けた企業アクション例】
- 省人化に直結する業務プロセスの棚卸し
- AI導入によるROI(投資対効果)の試算
- DXリーダー人材の育成・確保
- ロボット導入に向けた現場改革プロジェクトの立ち上げ
特に重要なのは、「自社にとってどの領域で機械化が最も費用対効果が高いか」を精緻に見極めることです。闇雲なAI導入ではなく、ピンポイントでの省人化と生産性向上が求められます。
2040年以降を見据えた製造業の未来シナリオ
2040年に向けて、日本の製造業は構造的な転換期を迎えることになります。
生産年齢人口は約6213万人に減少し、さらに2060年には約 4,800–5,000万人規模まで落ち込むと予測されています。この劇的な労働力減少に直面する中、製造業各社は「人手依存」から「機械前提」へとオペレーションを抜本的に変革せざるを得ないでしょう。
2040年代には、以下のような未来像が現実味を帯びると考えられます。
■ 製造業における未来の標準スタイル
- 人とロボットの協働が当たり前に
単純作業・反復作業はほぼ全てロボットが担い、人間は高度判断・管理監督に専念。 - 人型ロボット(ヒューマノイド)の実用化
従来の産業用ロボットに加え、柔軟な作業が可能な人型ロボットが本格投入される。 - フレキシブル生産ラインの普及
需要変動に応じて自在にラインを組み替えられる、AI制御型のスマートファクトリーが主流化。
こうした未来像の実現には、AIやロボティクス技術のさらなる進歩が欠かせません。特に、自律判断AI、予知保全機能の高度化、ロボットの自己最適化技術といった領域の発展が、労働力不足への決定打となるでしょう。
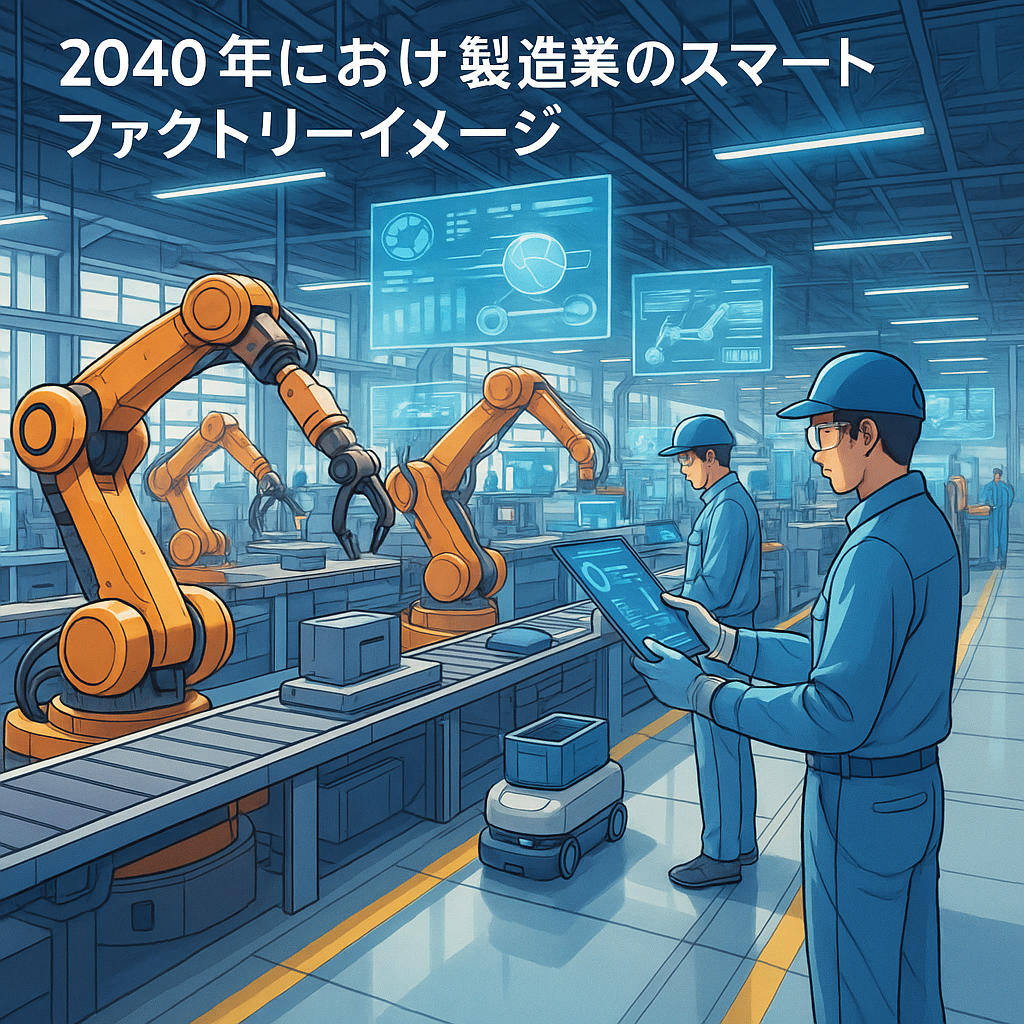
また、ビジネスモデル自体も変化する可能性があります。例えば、製品製造そのものをサービス化する「MaaS(Manufacturing as a Service)」モデルが普及し、受注生産やカスタム対応を自動でこなす企業が増えていくでしょう。
■ 2040年に向けた企業の備え
- 長期視点での自動化・AI投資計画の策定
- 人材ポートフォリオの見直し(「ヒト+機械」の最適化)
- リスキル教育の強化と現場マネジメント層のアップデート
特に、現場オペレーションだけでなく、経営戦略そのものが自動化前提で再設計される時代が到来します。経団連も「AI活用戦略Ⅱ」において「2040年までに社会全体でAI・ロボット前提の産業構造へ移行する」必要性を強調しています。
2040年以降、日本の製造業が生き残るためには、
単なる「作業の機械化」ではなく、ビジネスモデルごと機械時代に最適化する視点が不可欠です。
まとめ:製造業AI導入成功のために今できること
日本の製造業は、少子高齢化による労働力不足、国際競争力低下のリスク、そして2030年以降の人件費高騰といった課題に直面しています。これらを乗り越えるためには、AI導入と製造業自動化の推進が不可欠です。
ただし、単なる技術導入だけでは不十分です。
コスト逆転の転換点を見据え、今から以下の備えが求められます。
- 重点領域を絞った段階的な自動化
- 人材リテラシー向上への継続投資
- 長期ビジョンに基づくDX戦略の策定
AI導入は単なるコスト削減手段ではなく、企業の競争力そのものを左右する基盤になります。
いま行動を起こすことが、10年後、20年後の製造業における生き残りを決める鍵となるでしょう。
Footnotes
- Rakuten Group, Inc., Rakuten Survey Reveals AI Awareness Gap and Growth Potential for Japanese SMEs.
- KYODO NEWS, Less than 20% of Japanese firms using generative AI: survey.
- Robotics総研 手頃な価格で自動化を実現、協働ロボット導入が広がる背景とそのメリット.
- 湊ハマ株式会社 協働ロボット FAIRINO Robot.
- inbolt, Industrial robot cost decline
- Standard Bots, How much do robots cost? A detailed price breakdown for 2025.
- 国土交通省, 国土交通白書 2024, 第1節 本格化する少子高齢化・人口減少における課題 ■1 我が国の経済社会と人口減少
- 国立社会保障・人口問題研究所, 日本の将来推計人口(全国).
- 独立行政法人 情報処理推進機構, DX 動向 2024 – 深刻化する DX を推進する人材不足と課題.
- パーソル総研 X 中央大学 労働市場の未来推計 2030.